Therefore, in the cement manufacturing context, automation would mean a large-scale shift from labor-intensive methods to skill-intensive methods. The accelerated incorporation of real-time monitoring systems, advanced control systems would constitute the first step in realizing a genuinely 21st-century cement manufacturing process.
Besides bringing productivity gains, introducing automation would also push the entire industry towards being greener and more sustainable.
The Need for Automation in Cement Manufacturing
The cement industry faced a staggering decline in demand due to the pandemic, and the industry is notorious for being one where regaining lost revenues can take years. This has awakened stakeholders to the need for investing in intelligent systems that make cement manufacturing more agile and resilient to unexpected shocks in global demand.
As per Chatham House (a think tank), cement accounts for about 8% of global carbon dioxide emissions. As the world becomes increasingly aware of climate change and the need to reduce carbon footprints, cement manufacturers are constantly under pressure to invest in clean solutions to reduce their carbon footprints. Investing in computer-controlled carbon capture (CCUS) systems will allow manufacturers to meet stringent emission standards
Declining demand and decarbonization efforts will shift the emphasis from volume to value. Cement industries in the future will have to outline competitive advantages by way of decreased carbon footprints, improved decision-making systems, and continuous adjustments.
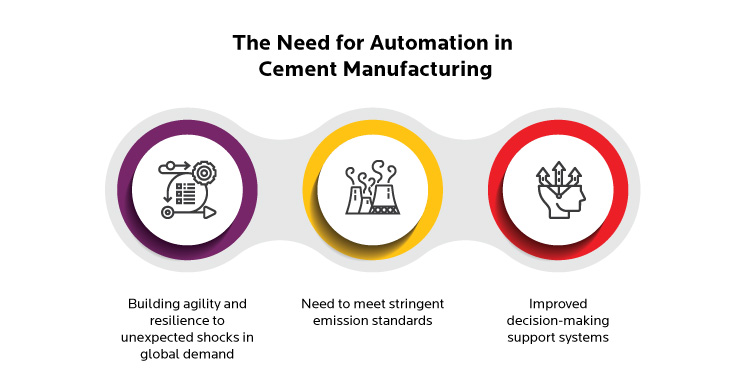
The need for automation in cement manufacturing
Automation Use Cases in Cement Manufacturing
Raw Material Transfer
In the initial stage of material extraction and transfer, the ingredients are first run through a primary crusher, after which they get transferred to a secondary crusher. These crushed materials are later placed in a stockpile where a stacker and reclaimer segregate the raw material as per the quality. It’s important to note that the stacking and reclaiming systems operate independently. These materials are then fused with specific additives to get the required cement composition. These additives are later transferred to different silos via different conveyor belts. Each of these silos is equipped with level detectors.
This entire process could be automated using a simple programmable-logic-controller (PLC) unit that could utilize censors to make real-time decisions depending on the input signals. An ideal setup would start at the press of a button that would initiate the transfer of raw materials to the crushers, both of which start with on-delay timers. This system can be extended till the final process of transferring the crushed material to the stockpile. In the event of an emergency shutdown, the operator will press a different button that will not only stop the initial conveyor belt but utilize the PLC to shut off subsequent systems sequentially.
Automation in Bucket Elevator, Screen Vibrator, etc.
The raw material transfer process is spread out over multiple stages. It initially begins with a transfer from the quarry to different silos, after which it is moved to homogenous silos. During the transfer to homogenous silos, a few key components such as the bucket elevator and screen vibrator are used, which can be further automated. Large granules that arise during this process are fed back to the vertical roller mill, and this process is known for creating hot, dusty air that is particularly hazardous to the environment. To prevent its release, this gas is sent through an Electrostatic precipitator (ESP) for purification, after which an ID Fan then removes the gas through the chimney.
This transfer process and its components lend themselves to further automation wherein the conveyor belts, bucket elevator, and screen vibrator are activated at the touch of a button. The operator will have to inspect prior processes before initiating this one. Delay timers will deactivate the bucket elevator, conveyor belts, and screen vibrator accordingly. When these processes are running efficiently, ESP and ID Fan are activated by the operator, which will trigger yet another conveyor belt for the final step of feeding dust back to the homogenous silo.
Cement Finishing Circuit
The cement mill (or finish mill) presents a convincing case for automation as the optimization process employed by many cement manufacturers is mainly manual. Particle fineness of the cement is measured by way of Blaine measurements, routinely carried out separately off-line. In a conventional setup, peak performance was ensured by manually adjusting the rate at which the clinker is fed, the separator speed, etc. These adjustments are made based on Blaine measurements and other routine plant-related variables, all of which provide the base for palliative action.
By employing a custom process automation system, this circuit could be set to self-adjust key parameters to maintain desired product quality, reduce variability, and improve operational stability. When customized according to the circuit’s requirements, such a scheme would outline a mathematical link between different parameters. Such a model would work in real-time and constantly keep pushing the plant towards operating in optimal capacity but within predefined limits.
Simultaneously, a steady-state optimizer would analyze the changes in the end product and effects changes in the control parameters to achieve optimal performance. Known as real-time receding horizon control, the process drastically reduces the need for manual intervention while improving product quality.

Automation use cases in cement manufacturing